Off-site manufacturing, modular and prefabricated building have been
transforming construction like nuclear fusion has been transforming energy:
they have both been twenty years away from working at scale for the last 60
years. The brutal economies of scale and scope in a project-based,
geographically dispersed industry subject to extreme demand swings have bought previous periods of success to an end, one reason the history of prefabrication features major
projects like the Great Exhibition in 1855 and more recently the Oresund Bridge
and Crossrail’s tunnels and stations. At an industry level, prefabrication has
been successful in specific niche markets, like institutional building in the
UK, or house manufacturers like the Japanese and Scandinavian firms Sekisui and
Ikea. The other problem at an industry level is the lack of standardisation,
although some countries such as the Netherlands try to address this through
their building codes.
Along the supply chain, however, many firms have integrated the various
technologies needed to produce building components and elements with the
barrier to entry, particularly for SMEs, the level of investment required. The
up-front capital requirements of prefabrication make it a capital-intensive
form of production, which brings high fixed costs in a cyclic industry
characterised by demand volatility over the cycle. This means the success or
failure of the underpinning business model can determine the success or
(typically) the eventual failure of the investment. A batch of new US prefab
housing firms went down after the GFC in 2007, for example,
demonstrating the importance of the relationship between the business model and
the viability of prefabricated building.
Another interesting characteristic of prefabricated building has been the
entry by large firms, sometimes from outside the industry, who have had the
capital to invest and an appetite for risk,
given that history. The recent news that Amazon has invested in a Californian prefabricated
housing manufacturer is therefore, possibly, important. Amazon is investing
heavily in smart home technology. This post also looks at two other firms that
are recent entrants into prefabricated and manufactured housing, UK insurance
company L&G, and vertically integrated US builder Katerra. Of particular
interest is the way these two companies are building volume, by developing a
pipeline of projects for their factories to supply. It concludes with a look at
the business model used for the mail order houses sold by Sears Roebuck a
hundred years ago in the US. By coincidence, this week Sears Roebuck missed a
debt payment and filed for bankruptcy, a reminder that no business model lasts
forever, no matter how successful.
Amazon
All the
large tech firms have venture capital subsidiaries that invest in early stage
start-ups. For Amazon it is the Alexa Fund, which provides funding for voice
technology innovation and ways to improve the way people use the technology. In
September, US start-up Plant Prefab had a $6.7 million Series A funding round
which included Obvious Ventures and the Alexa Fund. While this is Amazon’s
first investment in prefab construction, it has been selling tiny modular
houses made by MODS since last year.
Plant Prefab manufactures custom single and
multi-family homes in Rialto, California, using a patented building system. According to founder and CEO Steve Glenn, “Most existing
prefabrication companies in the US focus on standard, low quality,
non-sustainable mobile and modular homes -- for suburban communities. Plant
Prefab is unique in that we’re focused on custom, high quality, very
sustainable homes and we have a special facility and a patented building system
optimized for this. We build based on client’s architects or clients can select
from a growing number of homes we offer from world-class architects, all of
which can be customized for specific lots and client needs. By building in an
all-weather facility with lower cost and staff labour, we offer clients a more
reliable, time and cost-effective alternative to local, urban general
contractors.”
Amazon’s
investment in Plant Prefab comes with a new line of smart home
devices, suggesting the company sees a potential new market
driven by smart home technology. Amazon already has a deal with Lennar, the
largest homebuilder in the US, to pre-install
Alexa in all their new homes. There is an obvious business model here,
but also many possibilities. Amazon typically offers a combination of fee for service
and subscription services, which could be adapted for mortgage or rental
markets for example. As connectedness deepens and extends, Amazon might
potentially become a major player in the future residential building industry,
in some form.
Legal and General
Legal and General is a 180 year old British insurance company, today one
of the largest investment management firms in the world. In 2016
they announced plans to manufacture homes, however the opening of L&G’s
offsite housebuilding factory near Leeds has seen, and is seeing, many delays.
Although the first units were delivered in mid-2017, regular production is only
now being achieved and the factory is expanding. L&G is targeting
affordable housing, and set up a subsidiary called Legal and
General Modular Homes:
Our Vision is ambitious and is underpinned by our mission statement; “We
deliver desirable homes through the industrialisation of volume housing
supply”. Legal & General has a long heritage in providing housing in the UK
and sees modular construction as a natural evolution and extension of its
position in this market. Modular construction is set to revolutionise the house
building sector bringing new materials along with methods and processes used in
other industries, such as automotive and aerospace, to raise productivity and
help to address the UK’s chronic shortfall of new homes. Our investment in Europe's
largest modular homes factory demonstrates our ambition to inject capital into
the Housing sector alongside the creation of our Build to Rent, Later Living
and Housebuilding businesses. Located in Sherburn in Elmet, near Leeds, our
550,000 sq ft factory produces a range of typologies with the capacity to
produce up to 3,000 homes per year, employing several hundred local people.
The business model is this: “Legal & General Capital is building a more natural and sustainable model – one in which institutional investors are the long-term holders of the assets working alongside the best-in-class affordable housing operators who will provide the highest-quality housing management."
The business model is this: “Legal & General Capital is building a more natural and sustainable model – one in which institutional investors are the long-term holders of the assets working alongside the best-in-class affordable housing operators who will provide the highest-quality housing management."
L&G has
been investing heavily in the UK housing market over the last few years, and
aims to become the leading private affordable housing provider in the country,
with Legal & General Affordable Homes delivering 3,000 homes a year by
2022. They have a current pipeline of around 2,000 build-to-rent homes. And in
April 2018 L&G's investment arm bought the half share it didn’t own in
Cala, for £315mn, a property developer with a pipeline of 3,000 homes. L&G
also run retirement villages, they have 7 with 1,100 homes. By one estimate, L&G’s
total investment in build-to-rent currently stands at £1.5bn, with the aim to
have 6,000 homes in planning, development or operation by the end of 2019.
Katerra
Katerra is another Californian start-up, founded in 2015. In 2017 it
raised $130 million in a Series C funding round, reaching a $1 billion
valuation, The company’s goal is complete vertical integration of design and
construction, from concept sketches of a building to installing the bolts that
hold it together. On its projects the company is typically the architect, off-site
manufacturer and on-site contractor, and usually contracts directly with
owners.
The company started by developing the software to manage an extensive
supply chain for fixtures and fittings from around the world, but particularly China,
and then added a factory in Phoenix making roof trusses, cabinets, wall panels,
and other elements. In September2017 it announced plans to build a factory that will make
panels of cross-laminated timber, a high-tech structural wood, and later said
it planned to open up to seven more plants and warehouses around the US as the
business model gets rolled out.
One of the company’s three founders is a multi-family developer, and his
projects provided the initial pipeline of work that made the company viable.
Initially, buildings were designed by outside architects, but in 2016 the
company started a design division. In 2018, five months after raising another $865
million in venture capital from funders led by SoftBank’s Vision
Fund, Katerra acquired Michael Green Architecture and architects Lord Aeck
Sargent. The latter brings a healthy order book across a wider range of
buildings, the former is a leading advocate of CLT and high-rise buildings.
Katerra is essentially a technology play. A second founder has a tech
venture capital fund, the third and CEO did a stint at Tesla. Their ambition is
to leverage new technologies to transform building by linking design and
production through software. It designs buildings in Revit and then converts
the files to a different format for machines in the factory. Also, SAP HANA, a
real-time data processing application, and the Internet of Things are used to
achieve “deep integration and newfound efficiencies.” A nice time lapse of one
of their buildings is here:
Mail Order Houses
A bit over a century before Ikea sold their first Boklok house, one
fifth of Americans were subscribers to the Sears and Roebuck Mail Order
Catalogue. Anyone anywhere in the country could order a copy for free, look
through it, order something, and have it delivered to their door. At its peak
the Sears catalogue offered over 100,000 items on 1,400 pages, and in 1908 they
began offering houses.
While not the first company to sell kit homes by mail order, Sears came to
dominate the mail-order market. Between 1908 and 1940 it delivered 75,000 homes.
The Sears Modern Homes Program offered
complete houses, what would now be called ‘kit homes’. Customers selected from
dozens of different models, then they could order blueprints, send in a check,
and a few weeks later a train car would arrive with the door secured by a small
red wax seal. The new owner would open up the boxcar to find over 10,000 pieces
of framing lumber, 20,000 cedar shakes, and everything else needed to build the
home. The lumber came precut with an instruction booklet, and Sears promised
that, without a carpenter, a person could finish their mail order home in less
than 90 days.
Then, in
1911, Sears began offering mortgages to their customers. The Sears home
mortgage program became one of the keys to success (all those homes, and their
new, mostly young homeowners, needed furnishing and decorating and so on). In
lowering the barrier to entry, it allowed Sears to sell more kit homes faster
than any of its competitors. But when the Great Depression came things got
ugly, over the 1930s the company ended up foreclosing on tens of thousands of
its customers. It was a public relations disaster.
After years
of declining sales, Sears finally closed its Modern Homes department in 1940. A
few kit home manufacturers that hadn’t sold mortgages survived, but the
Sears boom was over. The next housing boom was the rise of the suburbs
and the prefab home. As demand surged in the postwar years, US companies such
as Lustron and the National Homes Corporation factory built homes by the thousands.
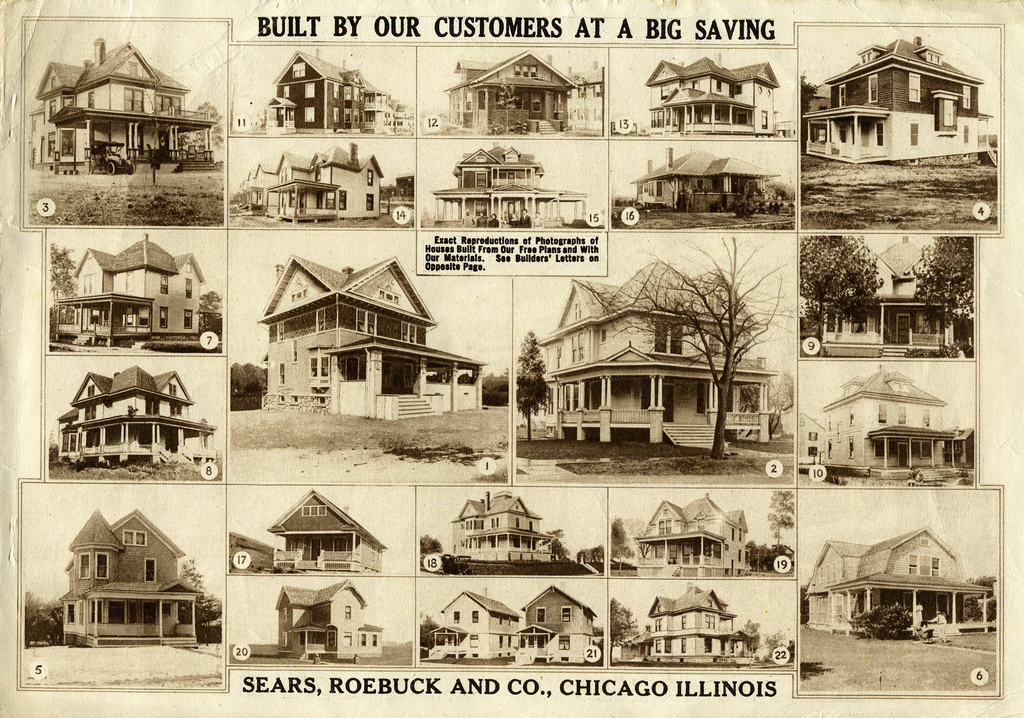